Dambrk Software Free Download
The TxDOT Bridge Geometry System(BSG) is used for bridge geometric design. The initial release of BGS, Version 8.1, was developed from the TxDOT Roadway Design System (RDS) Version 8.0 application by removing all non-bridge related RDS commands. The user may define, and display graphically, geometry points and curves, bridge alignments with templates, superelevation and widening, and bridge framing, with or without contours. The result of these changes to RDS is BGS, a 'scaled down' implementation of TxDOT RDS that focuses on bridge geometric design.An experienced RDS user will be able to begin using BGS immediately as BGS is used in the same way as RDS. The BGS and CAD plots are the same as RDS when applied to bridge geometric design.Processor:Memory:Free Disk Space:Operating System:Windows XP, Vista, 7Version: 8.1.7.2Date: Size:Prerequisite Software:The Bentley Systems MicroStation (V8-2004, V8-XM, or V8-i Edition) software must be installed in order to process BGS plot commands. Generalized beam-column discrete element model to analyze simple and continuous beam subjected to concentrated, uniform, uniformly varying, and non-uniformly varying static and movable traverse loads. The program considers the effect of axial load on stiffness.
It models spring supports, rotational spring restraints, and concentrated applied torques, It analyzes a beam-column of up to 999 discrete increments of user defined length. Flexural stiffness may be prismatic, uniformly varying, or non-uniformly varing.Processor: Pentium 133MhzMemory: 32mbFree Disk Space: 200kbOperating System: Win 32-BitVersion: 5.2.3Date: Size: 1.0mb. A specialized structural analysis program using a discrete element model that produces envelopes of maximum bending and shear forces acting on bridge bent caps. Analytical results are for working stress and/or load factor design in accordance with the AASHTO LRFD Bridge Design Specifications or the AASHTO Standard Specifications for Highway Bridges. Users input live loads are automatically placed within users defined lanes to generate maximum forces at users specified points.Processor: Pentium 133MhzMemory: 256mbFree Disk Space: 30mbOperating System:Windows 2000, 2003, XP, Vista, Windows 7Version: 6.2.2Date: 10/10/11Size: 1.4mb.
ConcreteWorks was developed at the Concrete Durability Center at the University of Texas as part of research funded by the Texas Department of Transportation (TxDOT). The system improves the constructability and durability of mass concrete bridge members and other structural members. Features include concrete mixture proportioning, thermal analysis, crack prediction, and chloride diffusion service life. It contains design modules for several mass concrete shapes, bridge decks types, precast concrete beams, and concrete pavements.Processor: see recommended minimum for OSMemory: see recommended minimum for OSFree Disk Space: 350 mb for installationOperating System: Win 2000, 2003, XP, VistaVersion: 2.1.3Date: Size: 171.5 mb.
CULV5 was developed and is maintained by the Texas Department of Transportation (TxDOT).CULV5 is an analysis tool for concrete box culverts. The program determines the forces acting on each of the different members of the culvert using the direct stiffness method. The user provides input data for loading conditions, structure geometry, and member sizes. The program outputs the member forces for use in either a working stress design or a load factor design in accordance with the AASHTO Standard Specifications for Highway Bridges, 17th Ed. For highway loadings, and AREMA 2006 in the case of E72 and E80 loadings.Processor: Intel PentiumMemory: 256mb (1GB recommended)Free Disk Space: 10mbOperating System:Windows (XP, Vista, or 7)Version: 2.2.2Date: Size: 1.6mb.
HY-8 is a computerized implementation of FHWA culvert hydraulic approaches and protocols. The HY-8 program is available at no charge to the hydraulic and transportation communities.The FHWA has been producing computerized culvert hydraulic software since the early 1960's (with the HY-1 program). The FHWA released the initial version of the HY-8 program in the early 1980's. FHWA released the original Windows version (7.0) in March 2007 and the second phase update (7.1) in July 2008.
The HY-8 program has successfully operated on all current 'flavors' of the Windows operating system.HY-8 7.2 represents a 'maintenance phase 'of the FHWA's multi-phase culvert hydraulic software upgrade plan. In the future, the plan calls for using a pooled fund effort1 to fund and support incremental upgrades and additions of features, based on available time, budget, and adoption of new hydraulic practices and techniques. (.pdf, 14 pages, 1 mb)Processor:Memory:Free Disk Space: 31 mbOperating System: Win 32-BitVersion: 7.2Date: 4/6/2011Size: 41 mb. This software has been collaboratively developed and maintained by the Washington State Department of Transportation (WSDOT) and TxDOT as part of the Alternate Route Project This TxDOT-customized version of PGSuper is a powerful, yet easy-to-use Windows-based program for design, analysis, and load rating of multi-span precast-prestressed bridge beams/girders in accordance with the AASHTO LRFD Bridge Design Specifications (1994-2012) and TxDOT design guidelines. Properties of TxDOT standard I girders (Tx Girders), U beams, Slab beams, Decked Slab beams, Box beams and X-Beams and TxDOT design criteria are included in templates and libraries published by TxDOT.The templates and libraries are managed and maintained by TxDOT and the software has the capability of dynamically and periodically updating the installed templates and libraries with the most current versions via the users Internet connection.
Custom defined beam shapes that fit within each family of girder types supported by PGSuper can also be added to a users copy of the templates, thereby extending the girder shapes that the user can design and analyze with the program.The flexural design feature computes the number and configuration of prestressing strands and the minimum required release and final concrete strengths. PSTRS14 has been developed and is maintained by the Texas Department of Transportation (TxDOT). SignsPC - TxDOT Traffic Sign Detailing ProgramThe SignsPC application is used in conjunction with the MicroStation computer-aided drafting application. SignsPC extends MicroStation by providing the user with a toolkit for generating and labeling traffic signs. The toolkit also includes a lettering feature to accurately place lettering cells spaced according to standard specifications.Processor: Determined by MicroStation requirementsMemory: Determined by MicroStation requirementsFree Disk Space: 10mbOperating System:Windows (XP, Vista, or 7)Version: 3.2.4Date: Size: 5.0 mbPrerequisite Software:The Bentley Systems MicroStation (V8-2004, V8-XM, or V8-i Edition) software must be installed on the destination computer in order to install and run SignsPC. For use only by Engineering Consultants under contract to TxDOT to perform shop plan review. The Shop Plan Review Tools add-in for Adobe Acrobat Professional provides functions to expedite approval stamp placement, hiding/showing reviewer markups, and document flattening.
Prior installation of Adobe Acrobat Professional 7.0, 8.0, or 9.0 is a prerequisite.This add-in has been tested for compatibility with Adobe Acrobat Pro versions 7 through 9. It is advisable to ensure that critical markups are retained on plan sets when using different versions of Adobe Acrobat Pro.(This product remains unchanged from its previous listing as simply 'ShopPlanTools' prior to the posting of 'SPRT - Shop Plan Review Tools for Acrobat Pro 10'. This version of Shop Plan Review Tools will NOT work with Adobe Acrobat Pro 10.)For questions or comments, contact Jeff Cotham at Jeff.Cotham@txdot.gov.Processor: PentiumMemory: 128mbFree Disk Space: 246kbOperating System: Win 32-BitVersion: 1.0.2Date: 6/15/2009Size: 0.36mb. For use only by Engineering Consultants under contract to TxDOT to perform shop plan review. The Shop Plan Review Tools add-in for Adobe Acrobat Professional provides functions to expedite approval stamp placement, hiding/showing reviewer markups, and document flattening. Prior installation of Adobe Acrobat Professional 8.0, 9.0 or 10.0 is a pre-requisite.This add-in has been tested for compatibility with Adobe Acrobat Pro versions 8 through 10.
It is advisable to ensure that critical markups are retained on plan sets when using different versions of Adobe Acrobat Pro.(The older Shop Plan Review Tools for Acrobat Pro 7 will not work with Acrobat Pro 10. The necessary changes incorporated into this product for Acrobat Pro 10 compatibility, however, do not prevent it from working with Adobe Acrobat Pro 8 and 9 also.)For questions or comments, contact Jeff Cotham at Jeff.Cotham@txdot.gov.Processor: PentiumMemory: 128mbFree Disk Space: 246kbOperating System:WindowsXP, Windows7-32, Windows7-64Version: 1.1.0.1Date: Size: 0.36mb.
TBLRP - Texas Bridge Load Rating ProgramThe Texas Bridge Load Rating Program (TBLRP) uses a working stress (WS) analysis method which produces an allowable stress load rating. This load rating methodology is in accordance with the AASHTO Manual for Condition Evaluation of Bridges, 1993, and the AASHTO Standard Specifications for Highway Bridges, 14th Ed., 1989. This program simplifies the load rating of nonstandard bridges that are commonly found on rural roads off the state and federal highway systems. The program emphasizes standardized and efficient load rating with a goal of minimizing clerical and computational errors inherent in manual methods.Processor: Pentium 133MhzMemory: 3mbFree Disk Space: 4mbOperating System:Windows XP, Windows 7Version: 6.1.4Date: 10/05/12Size: 1.8mb.
The TxDOT Bridge Toolbox (TxBridge) software is used in conjunction with the Bentley(R) Systems MicroStation(R) computer-aided drafting application. TxBridge extends MicroStation by providing the user with various utilities that implement CAD standards adopted by the TxDOT Bridge Division. These utilities automate the selection of drawing scales and the placement of text and terminator elements.Processor: Determined by MicroStation requirementsMemory: Determined by MicroStation requirementsFree Disk Space: 10mbOperating System:Windows (XP, Vista, or 7)Version: 1.5.5.1Date: January 2012Size: 1.2 mbPrerequisite Software:The Bentley Systems MicroStation (V8-2004, V8-XM, or V8-i Edition) software must be installed on the destination computer in order to install and run TxBridge. This software product was developed and is maintained by the University of Texas at Austin.
UTCGAT is a suite of software tools for the analysis of curved girders. The suite consists of UT Bridge and UT Lift.UT Bridge is a 3-dimensional finite element program for the analysis of curved steel I-girders. Computations include linear elastic analysis and eigenvalue buckling analysis for both girder erection and concrete deck placement.UT Lift is an easy to use, macro-programmed Excel spreadsheet for determining the safety of lifting a horizontally curved steel I-girder with one crane and two lift clamps.Processor: Pentium 133 MhzMemory: 1 GB (will run on 512 MB but slowly)Free Disk Space: 50 MBOperating System:Windows 7, XPVersion: 1.1.0Date: Size: 44 MB.
IntroductionThis document provides an overview of consequence classification for dams in BritishColumbia. It outlines a rough method for assessing consequence and some key conceptsthat require consideration in assessing consequence. If the method provides a clearlydefined consequence classification then a consequence classification can be assigned. Ifthe results are uncertain, use of the higher possible consequence classification isappropriate or a more detailed assessment method should be used. For larger structures orcomplicated downstream channel conditions more detailed procedures may be requiredThese guidelines are only intended for consequence of failure classification.
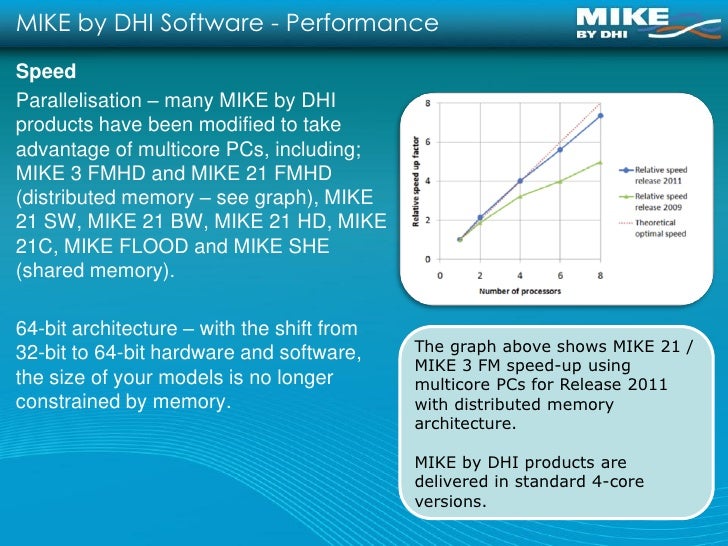
They are not adequate for the preparation of inundation mapping for Emergency Preparedness Planning (EPP), or for the assessment of hazards and risk analysis. The flood hydrograph resulting from a dam breach is dependent on many factors. The primary factors are the physical characteristics of the dam, the volume of the reservoir, and the mode of failure. The dam characteristics such as dam geometry, construction materials, and mode of failure; determine the dimensions and timing of breach formation.
Breach formation, volume of reservoir storage, and reservoir inflow at the time of failure determine the peak discharge and the shape of the flood hydrograph. The following sections provide a method for estimating dam breach parameters and peak flow discharges for earthfill dams. Earthfill dams are focused on because the great majority of small dams are earthfill. When estimating concrete gravity dam breach parameters, a complete failure of a discrete number of monoliths is considered. For concrete arch dams a complete dam failure is considered. Breach times for concrete gravity dams generally fall between 0.1 and 0.5 hours and for concrete arch dams they generally fall between instantaneous and 0.1 hours. Estimation of Dam Breach Parameters.
There are a number of methods for modelling the attenuation of peak flow as the breach flood wave travels downstream. For consequence classification a simplified procedure based on generalised flood attenuation curves developed by the USBR (1982) is often adequate. The curves presented in Figure 1 should be used conservatively as they utilize generalised solutions to approximate the reduction of flood peak discharge with distance downstream of the dam. For example the attenuation would be much smaller for a dam breach flow travelling down a steep narrow valley. Once the dam breach flood inundation path has been determined, the resulting consequence of failure classification can be determined. For BC, the classification system is outlined in Schedule 1 “Downstream Consequence Classification Guide” of the British Columbia Dam Safety Regulation.
Refer to the Regulation for Schedule 1. The highest consequence rating in one of the three categories; loss of life, economic and social loss, and environmental and cultural losses is the consequence rating for the dam. ConcreteConcrete is an intimate mixture of:Cement,Sand (Fine Aggregate),Coarse Aggregate,Water.New Generation Concrete needs use of SpecialMaterials in addition to above i.e. Tile drainage(in ) is an agriculture practice that removes excess water from soil subsurface.
Whereas is the practice of adding additional water when the soil is naturally too dry, drainage brings soil moisture levels down for optimal crop growth. While surface water can be drained via pumping and/or open ditches, tile drainage is often the best recourse for subsurface water. Too much subsurface water can be counterproductive to agriculture by preventing root development, and inhibiting the growth of crops. Too much water also can limit access to the land, particularly by farm machinerySub Surface/ Tile Drainage SystemSoftware for Tile Drainage/ Sub-Surface Drainage to determine Drain Spacing. For nearly 30 years, ETABS has been recognized as the industry standard for Building Analysis and Design Software. Today, continuing in the same tradition, ETABS has evolved into a completely integrated building analysis and design envir onment. Stream flow records are primarily continuous records of flow passing through a particular section of the stream.
Stream flow data are analyzed to determine the magnitude and variability of surface waters. These records are input in planning, design, and operation of surface water projects and are also used in design of bridges and culverts, flood forecasting systems, and flood plain delineation. The sections where canal measurements are carried out are known as canal gauging stations.
A network of these stations is established to collect data about surface water resources of a region. There exists a relationship between stage and discharge at a section.

This relation is termed as stage-discharge relationship or rating curve. The two most significant flow regimes under which any open channel constriction may operate are free flow and submerged flow. Other terms for free flow are critical depth flow and modular flows, while other terms for submerged flow are drowned flow and non-modular flow. The distinguishing difference between the two flow conditions is the occurrence of critical velocity in the vicinity of the constriction (usually a very short distance upstream of the narrowest portion of the constriction). When this critical flow control occurs, the discharge is uniquely related to the depth or “head” upstream of the critical section. Thus, measurement flow depth at some specified location upstream from the point of the critical condition is all that is necessary to obtain the free flow discharge. The size of the crew depends on the speed at which the team should work.
A team for man, a 5-man survey crew, a 2-man hydrographer team, a 12-man flume measurement team, driver and a couple of casual laborers could cover one or two canal circles a year. Reductions would obviously decrease the work rate. A 6 to 7-man crew should be adequate at the division level; says foreman, surveyor, hydrographer and 3 to 4 assistants. The number of assistants depends somewhat on the number of portable flumes to be used. A 3-man crew appears to be the minimum requirement. A primary objective of this lecture is to make minimum use of existing facilities for water measurement.
This will require calibration and rating of various hydraulic structures. The primary problem will be submerged flow conditions. Unfortunately, in many cases, submergence may exceed 95 percent, making measurements less reliable. It is expected that gated and up gated head works for distributaries as well other water control structures will form the basis of measurement discharge stations.
The outfall points of sub drains branch drains and main drains would be best measurement sites for drainage discharge. Initially the discharge measurements are made with the frequency necessary to define the station rating, as early as possible, over a wide range of stages.
Measurements are then made at periodic intervals to verify the rating or to define any changes in the rating caused by changes in the stream channel. Monthly observations of canal/drain discharge are generally sufficient, though daily data are needed to calculate the statistical parameters of the discharge.
Manual water discharge observations are still in practice. However, in many countries even paper systems for continuous data recording have been almost entirely replaced by largely automated electronic logging, analysis and data transmission systems.
In general, flows are measured at any point where the conveyance system flows are divided between two or more channels. As an everyday procedure, flows are not directly measured into watercourses. Flows should normally be measured into all canals/drain, although there are cases where it is not practical to measured flows in main or branch canals/drains each time a small distribuaery is measured. The flow in the main canal would be measured at the next downstream control structure and at outfall points in case of drains. Discharge measurements by the current-meter method are made from a boat, from a cable or bridge or by wading the stream. In irrigation canals mostly the boat measurements are employed for the purpose.
The measurement need not to be made at the exact location of the gauge because the discharge is normally the same as at the gauge throughout a reach of channel in the general vicinity of the gauge. Discharge measurements of the highest accuracy will be obtained at cross-sections having the following characteristics. Current meters are velocity measuring devices that sample at a point.
Each point velocity measurement is then assigned to a meaningful part of the entire cross section passing flow. The velocity-area principal is used to compute discharge from current-meter data. Total discharge is determined by summation of partial discharges. Data are usually determined over a useful range of total discharges. These discharges are related to measured water surface elevations related to a fixed head measuring device to provide a rating curve. After full confidence in the rating is attained, the calibrated. Anemometer and propeller current meters are the most common type used for irrigation and watershed measurements.
These meters use anemometer cup wheels or propellers to sense velocity. The Price current meter and the smaller pygmy meter modification are the most common current meters in use.
These meters are rated by dragging them through tanks of still water at known speeds. The reliability and accuracy of measurement with these meters are easily assessed by checking mechanical parts for damage and using spin-time tests for excess change of bearing friction. This type current meter does not sense direction of velocity, which may cause problems in complicated flow where backflow might not be readily apparent. For irrigation needs, this problem can be avoided by proper gage station or single measurement site selection. Doppler type current meters determine velocity by measuring the change of source light or sound frequency from the frequency of reflections from moving particles such as small sediment and air bubbles. Laser light is used with laser Doppler velocimeters (LDV), and sound is used with acoustic Doppler velocimeters (ADV).
Acoustic Doppler current profilers (ADCP) have also been developed. These instruments measure average velocities k of cells of selected size in a vertical series. Thus, they measure vertical current profiles. ADCP measurements are becoming more frequent for deep flow in reservoirs, oceans, and large rivers. Most of the meters in this class are multidimensional or can simultaneously measure more than a single directional component of velocity at a time. The main external components of an ADCP are transducer assembly and a pressure case. The transducer assembly consists of four transducers that operate at a fixed, ultrasonic frequency, typically 300, 600, or 1200 kilohertz (kHz).
The transducers are horizontally spaced 90 degrees apart on the transducer assembly; all transducers have the same fixed angle from the vertical, referred to as a “beam angle,” that is typically 20 or 30 degrees. The transducer assembly may have a convex or concave configuration. The pressure case is attached to the transducer assembly and contains most of the instrument electronics. The ADCP measures velocity magnitude and direction using the Doppler shift of acoustic energy reflected by material suspended in the water column.
The ADCP transmits pairs of sort acoustic pulses along a narrow beam from each of the four transducers. As the pulses travel through the water column, they strike suspended sediment and organic particles that reflect some of the acoustic energy back to the ADCP.
The ADCP receives and records the reflected pulses. The reflected pulses are separated by time differences into successive, uniformly spaced volumes called “depth cells.” The frequency shift (known as the ‘Doppler effect”) and the time-lag change between successive reflected pulses are proportional to the velocity of the scatters relative to the ADCP. The ADCP computes a velocity component along each beam; because the beams are positioned orthogonally to one another and at a known angle from the vertical (usually 20 or 30 degree), trigonometric relations are used to compute three-dimensional water-velocity vectors for each depth cell. Thus, the ADCP produces vertical velocity profiles composed of water speeds and directions at regularly spaced intervals.
Optical strobe velocity meters developed by the U.S. Geological Survey (USGS) and the California Department of Water Resources use optical methods to determine surface velocities of streams (USGS, 1965).
This meter uses the strobe effect. Mirrors are mounted around a polygon drum that can be rotated at precisely controlled speeds. Light coming from the water surface is reflected by the mirrors into a lens system and an eyepiece.
The rate of rotation of the mirror drum is varied while viewing the reflected images in the eyepiece. At the proper rotational speed, images become steady and appear as if the surface of the water is still. By reading the rate of rotation of the drum and knowing the distance from the mirrors to the water surface, the velocity of the surface can be determined. The discharge rate of the stream may be estimated by applying the proper coefficient to this surface velocity and multiplying by the cross-sectional area of the flow section. The changing nature of some rivers and canals may require frequent current-meter measurements. Sand shifts may occur frequently, often daily, and aquatic weeds may continue to grow and increase in area. To obtain the gage-discharge relationship at stations on such streams, current-meter measurements may be necessary two or three times weekly or perhaps daily if the importance of equitable water distribution justifies such action.
A rating section consisting of a short-lined section in a straight stretch of channel will ensure a meter station of unvarying dimensions if the sediment problem is not serious. Pygmy meters are similar to Price meters in that both contain a cup-type wheel mounted on a vertical shaft. The pygmy cup wheel is 2 in diameter, compared with 5 in for conventional Price meters. Thus, the pygmy meter can measure velocities closer to flow boundaries. The contact chamber is an integral part of the yoke and contains a single-revolution contact only. The meter has no tailpiece, and no provision is made for cable suspension.
The rotational speed of the pygmy meter cup wheel is more than twice that of Price meters. Consequently, use of the pygmy meter is limited to velocities up to 3 or 4 ft/s. The pygmy meter was specially designed for use in small, shallow streams. The smaller meter was necessary because a standard. Price meter does not perform with sufficient accuracy when it occupies a good share of the available stream depth. The pygmy meter may also be used in large canals where the velocity of flow is low or near the edges of a canal to supplement data taken farther out in the channel with a Price meter. In special situations, Reclamation has used meters of the propeller type with horizontal axles.
Hoff meters, Haskell meters, Ott meters, and Neyrpic 'Dumas' meters are examples. An assembly of eight Dumas meters with appropriate handling equipment is shown on next page. In this case, the equipment was mounted on a flatbed truck for positioning. These meters have some advantages compared to the Price meters. They are less sensitive to velocity components not parallel to the meter axis, they are smaller, and they are more suited for mounting in multiple units. Current meters must receive the best care during transportation and use to ensure accurate velocity measurements.
Particular care should be taken when working near bridge piers and abutments, floating debris, and also when measurements are being taken at irregular or unknown sections and the meter is suspended on a measuring line. If the cups or blades become bent or damaged, the results obtained from the rating curve for the meter will be unreliable. After completing the measurements at a rating station, the meter should be carefully cleaned. After each day's use, it should be properly lubricated. Discharge measurement using current meter is accomplished by measuring velocity and area. The depth of flow in the cross section is measured at width stations with a rod or sounding line.
As the depth is measured, observations of velocity are obtained with the current meter at one or more points in the vertical. The measured widths, depths and velocities permit computation of discharge for each sub-area of the cross-section.
The summation of these sub-areas discharge is the total discharge of channel. The number of revolutions of the rotor is obtained by an electrical circuit through the contact chamber of the current meter. Contact points in the chamber are designed to complete an electrical circuit at selected frequencies of revolution.
Contact chamber can be selected having contact points that will complete the circuit twice per revolution, once per revolution, or once per five revolutions. The electrical impulse produces an audible click in a headphone or registers a unit on a counting device. The counting intervals are measured by a stopwatch. The vertical-axis current meter, the Price meter, type AA which is extensively used by the US Geological Survey (USGS). The standard price meter has a rotor, 5 inches in diameter and 2 inches high with six cones shaped cups mounted on a stainless steel shaft. A pivot bearing supports the rotor shaft.
The contact chamber houses the upper part of the shaft an eccentric contact that wipes a bead of solder on a slender bronze wire (cat’s whisker) attached to the binding post. A separate reduction gear (pent gear), wire and binding post provide a contact each time the rotor makes five revolutions. A tailpiece keeps the meter pointing into the current direction. Accuracy of a discharge measurement depends, in part, on the number of verticals at which observations of depth and velocity are obtained.
In general, the interval between any two verticals should not be greater than 1/20-th of the total width, and the discharge between any two verticals should not be more than 5 percent of the total discharge. Observation verticals should be located so as to best define the variation in elevation of the stream bed and the horizontal variation in velocity.
Fewer verticals are required on very small streams, since the intervals between any two verticals must be greater than the diameter of the current-meter propeller. The number of verticals should be increased for the first few measurements at a new state. The depth may also be measured with an echo (sonic) sounder. The transducer is usually mounted on the boat, submerged about 1 foot below the water surface, and the depth read from a strip-chart recorder.
With previous models of sonic sounders, regular calibrations were required under the same conditions of salt content and water temperature as are encountered in the measurement. However, with the latest versions (such as Raytheon DE-719 B) the instruments are provided with compensatory adjustment devices, thus requiring very calibration. In the two-point method of measuring velocities, observations are made in each vertical at 0.2 and 0.8 of the depth below the surface. The average of these two observations is taken as the mean velocity in the vertical. This method is based on many studies of actual observation and mathematical analysis.
Dambrk Software Free Download
Experience has shown that this method gives more consistent and accurate results than any of the other methods except the vertical velocity curve method. The two point method is the one generally used. Measurement of discharge from a boat is generally made either on channels that can be readily spanned by a temporary cable of sufficient strength to hold the boat in position while measurements are made, or rivers where a cable cannot be stretched. In such rivers, the boat is equipped with a facility (motor boat engine or anchor) to keep it temporarily positioned in the stream.
On channels where cable can be stretched horizontal distances (widths) are measured by affixing graduations on the cable. On channels without cable, the widths are either measured by the observer in the boat or by an observer on the bank. For the purpose, points are fixed on the bank(s) along the line of sight and perpendicular to it.
The boom part consists of two structural aluminum channel shapes, one telescoped within the other, to permit adjustment in length. The boom has a pulley at the upstream and to guide the sounding cable and base on the downstream end to the fix the real. The cross-arm called ‘horizontal stabilizer’ constructed of structural aluminum channel, is fixed to the gun-whales of the boat by J-bolts. At both ends of the arm, there are guide sheaves under which the boat tagline is passed.
There is also an arrangement to clamp this arm with the stretched tagline to keep the boat stationary at a desired position. A sounding real has a drum for winding the sounding cable, a crank and ratchet assembly and a depth indicator.
Five types of reels are available i.e. A, B.C, D and E. All reels are similar in that these are fitted with a depth indicator, a treading sheave for laying the cable smoothly in a single layer on the drum, electrical connections for two conductor cables and a pawl and ratchet which can be used to hold the current meter and weight at any desired elevation. All the reels are made largely of aluminum for lightness and designed to operate under any load to the full strength of the cable ordinarily used. A, B and E type reels have the same spacing of anchor studs, so that they are completely interchangeable.
D type reel is larger and is used for heavy weights only. Columbus-type fish weights suspended with cable are used to sound depth as well as to suspend the current meter in the moving stream. These are commonly known as C-type weights and maintain a steady position in water flowing at high velocities.
These are available is sizes of 15, 30, 50, 75, 100, 150, 20 and 300 pounds. The nose of each weight extends beyond the cups of the current meter and hence affords protection against any damage. 15-pound weight is a one-piece casting of gun-metal bronze.
All the other sizes are cast from lead and contain removable aluminum-alloy tail vanes. The shape of the slot for the hanger-strap permits it to tip forward 15o and backward 5o from the vertical.
This limitation in the angles prevents the weight and current meter from striking each other. Due to some variation in the quality of material used in construction, it is necessary and describes that the weight be balanced under water, regardless of level position it assumes when suspended in air. The hanger strip is used for carrying the current meter, its lower end is fixed with the sounding weight and the upper end to the cable through a connector. It is 1/8 inch thick, 1-1.5 ft long and made of steel.
It contains a hole threaded for a 3/8 inch hole at the opposite end. Three holes, 7/32 inch in diameter, are at 4,9,5,3 and 9.8 inches above the hole for weight suspension. The lower two of these are used for supporting the current meter so that its horizontal axis is 0.5 ft from the bottom of C-15 and C-30 respectively. The third hole is located so that the distance from the horizontal axis of the meter to the bottom of the C-50 or heavier weight is approximately one foot. The velocity of flow in a canal or canal/drain, and hence the discharge may be determined approximately by the use of float.
A stretch of the canal, straight and uniform in cross-section and grade, and with a minimum of surface waves, should be chosen for this method. Surface velocities only be attempted on windless days to avoid wind-caused deflection of floats. Even for best conditions, surface floats are diverted from a direct course between measuring stations because of surface disturbances and cross-currents. In addition to surface floats, which are immersed one-fourth or less of the flow depth, rod floats, which are submerged more than one-fourth of the depth but not touching the bottom should be used.
In general, because a number of other methods are easier and more accurate, this method should be used when other methods are impossible or impracticable. Hence this method is not suitable for calibrating the Indus Systems structures. The two-tenths, three-point, and one-point continuous methods are special procedures based on a relationship previously established for the section between the true discharge and the velocities observed by these methods. These methods are generally reliable for sections which undergo no serious changes because of erosion, sedimentation, or other deformation. They are discussed in detail in USGS (1965) and USGS (1980).
Of the methods cited in this section, the two-point method and the six-tenths-depth method are most used in canal work. Q = the discharge in cubic feet per second (ft 3/s) for a partial areaQ = total discharge= the mean velocity associated with the partial areaa = partial area of total cross sectionL 1, L 2. L n = distance to vertical measurement locations in feet from an initial point to vertical stationL = the distance in feet between consecutive vertical measurement stations,. = the respective mean velocities in feet per second at vertical measurement stationsD 1, D 2. D n = the water depths in feet at verticalsn = the number of verticals related to the partial area. In the midsection method, the depth and mean velocity are measured for each of a number of verticals along the cross section.
The depth at a vertical is multiplied by the width, which extends halfway to the preceding vertical and halfway to the following vertical, to develop a cross-sectional area. The product of this area and the mean velocity at the vertical gives the discharge for the partial section between the two halfway points. A summation of the partial discharges gives the total discharge. The formula for computing the partial discharge using the midsection method is. In this method, Simpson's parabolic rule is used twice to compute discharge using the area velocity method. First, the area is computed for three consecutive depths at velocity measuring stations using Simpson's rule. Second, average velocity for the same three verticals is computed by the rule.
The discharge between the three verticals is the product of the average velocity and area. Using Simpson's rule assumes both the vertical depths and their corresponding average velocity vary parabolically.
Natural riverbeds and older earth-lined canal bottoms follow curved shapes rather than the typical straight line geometry of hard-lined canal designs. Both vertical and horizontal velocity profiles tend to be parabolic in either case. Using Simpson's rule to obtain the area between three equally spaced consecutive verticals or two consecutive partial areas results in. The canal bed at a well selected current-meter station is generally permanent in character, and a permanent rating curve could be made if not for sediment accumulations or for growths that occur in the canal during the irrigation season. The sediment and the growths both decrease the discharge capacity of the canal for all flow depths, and the effect is usually most pronounced during the latter part of the irrigation season. This change in flow capacity of the canal for a given depth of flow must be taken into consideration when computing the quantity of water carried by the canal.
If the canal is cleaned during the season, the relationship of discharge to gage height is again disturbed. The changing relationship of discharge to gage height in irrigation canals caused by changing boundary conditions is the chief source of error in flow measurements. To determine the quantity of water carried by a canal over a period of time, the gage must be read at least twice daily. More than one reading provides a means for checking the readings and also informs the canal attendant of any unexpected changes in canal stage. More frequent readings are needed when changes in stage are suspected or are made in the canal.
The readings should be taken by the canal attendant on regular rounds. The gage should be read accurately, generally to the nearest hundredth of a foot. Automatic water-stage recorders eliminate the need for numerous readings and can increase the accuracy of the flow measurements. Finally, the discharge curve is drawn through the computed discharge points. If flow conditions in the channel did not change resistance significantly during the period needed for measurements over the full range of canal flows, the curve will generally be easy to draw. If the relationship of discharge to gage height was affected by growths or sediment deposits, one or more additional discharge curves must be drawn. The number of rating curves required for a cross-section location depends upon the degree of the flow restric- tions encountered and the rate at which the restrictions developed.
These curves will generally be parallel to, but slightly displaced from, the curve for the clean canal. For the periods when the change is in progress, discharges may be estimated by proportioning between curves for the clean and restricted conditions on a time basis. From the rating curve, a rating table may be prepared for each tenth or hundredth of a foot of gage height from zero to the maximum height of water in the canal or stream. For canals affected by growths or sediment, two or more such rating tables will be necessary, one for early in the season when the canal is clean, and the other for late in the season when growths or other restrictions are present.
If the canal is cleaned during the irrigation season, operating personnel should be instructed to switch to the curves and tables for the clean canals.